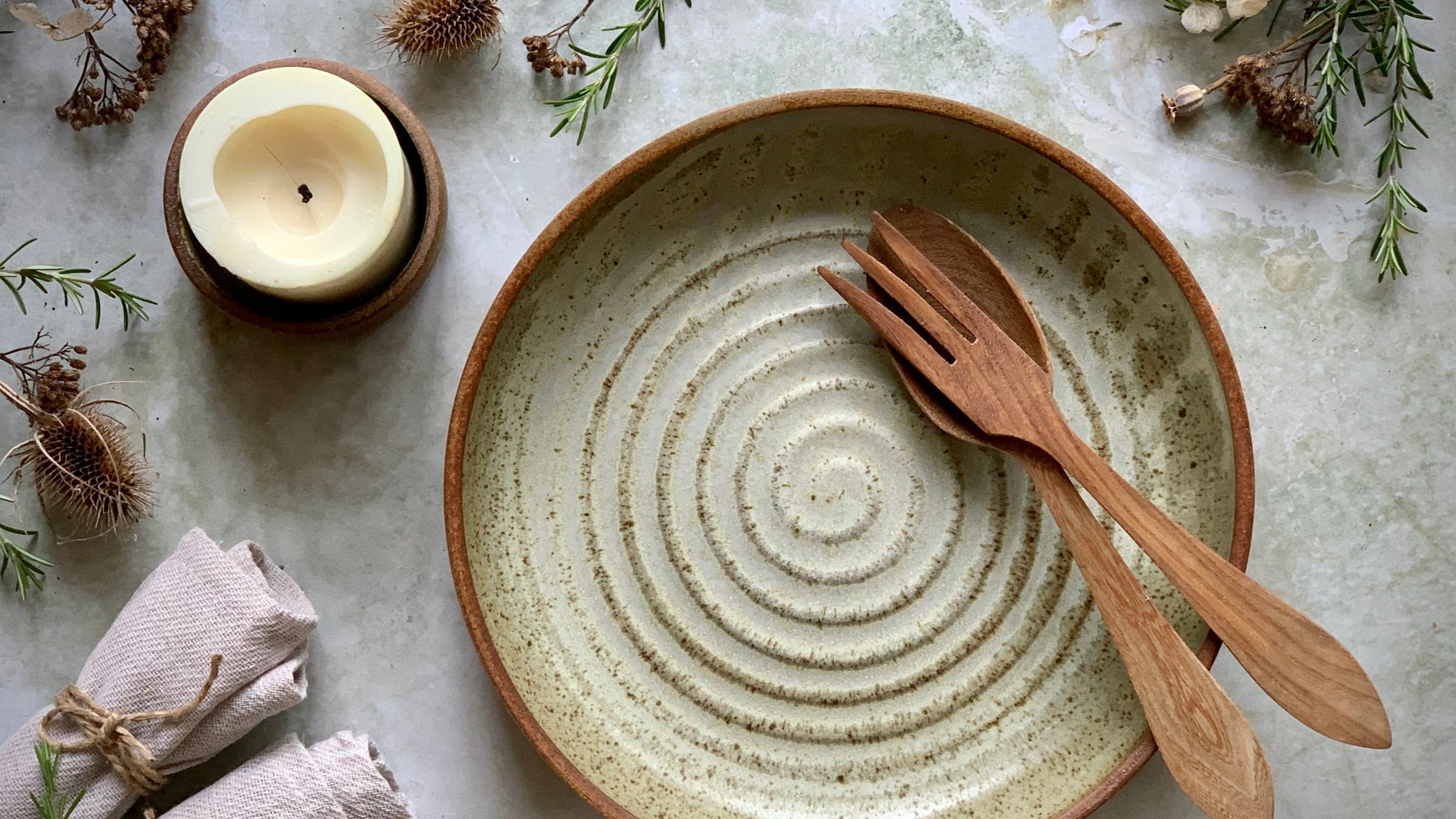
Wood-fired Collection
Earthy, organic, completely individual ceramics
I am very lucky to be able to make wood-fired collections, thanks to being part of a local group of potters who fire a couple of times a year. This traditional technique that is now only used by a few potters. It’s a labour of love as each firing can takes days, yet whilst its fraught with uncertainty, the beautiful individual and unique pots that emerge are worth the effort. Organic earthy finishes from ash circulating in the kiln landing on the pots to create beautiful speckles and glaze effects while flames ‘toast’ unglazed clay surfaces.
The wood-fired collections are usually released twice a year (Spring and Autumn).
Discover more about this traditional firing technique
Wood-firing is an ancient technique used for centuries throughout the world, however it is now only practised by a few potters. Its incredibly time consuming, taking days to load and fire, requires a team of potters to work together and a large amount of ‘zen’ calm as the results can be so unpredictable yet worth every minute!


Wood-fired kilns vary in shape and design, ours is a large down-draught design that holds hundreds of pots in a chamber above two fire boxes. Loading the kiln takes days and a very careful hand as the shelves are built up around the pots in two layers at the back and front.
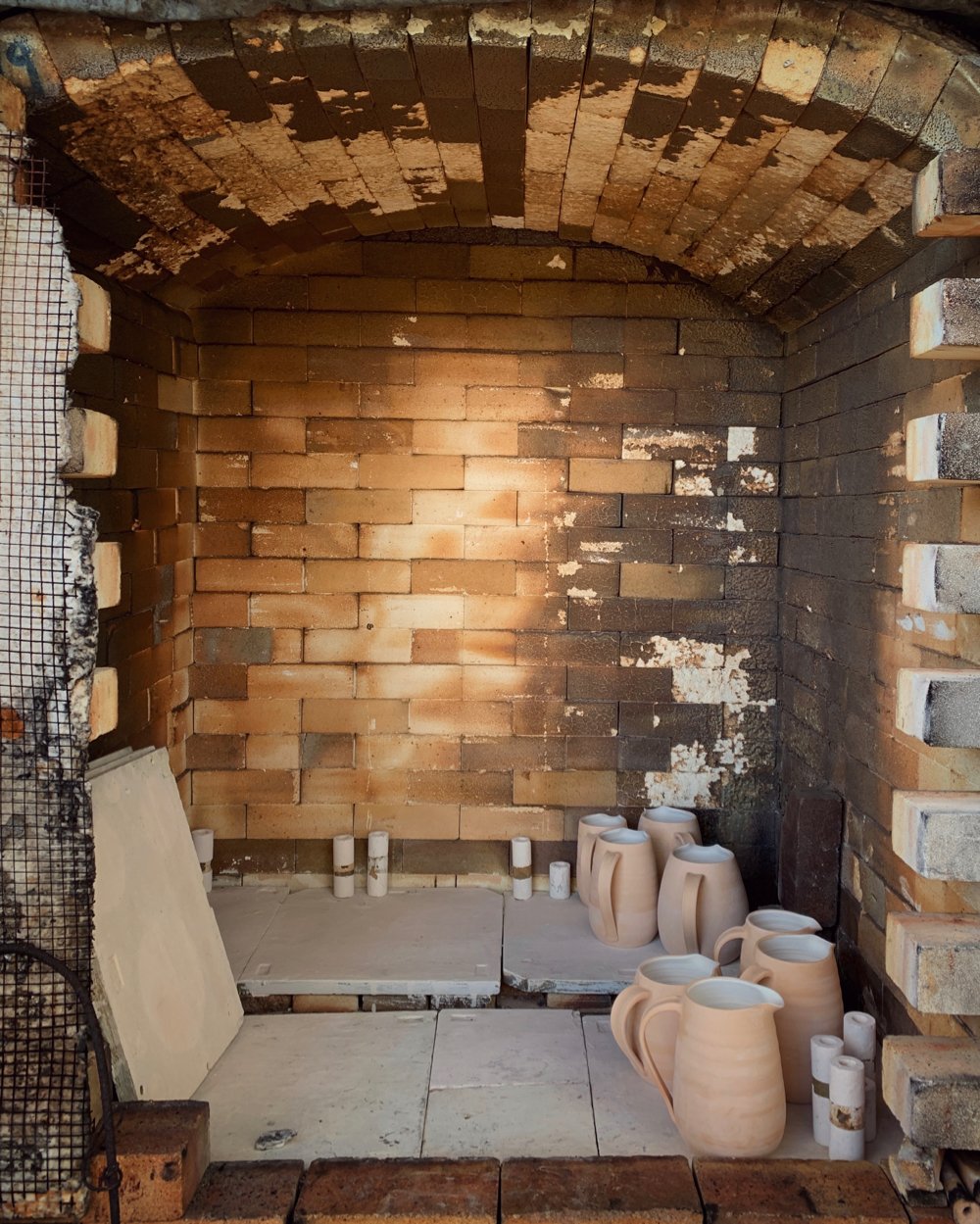
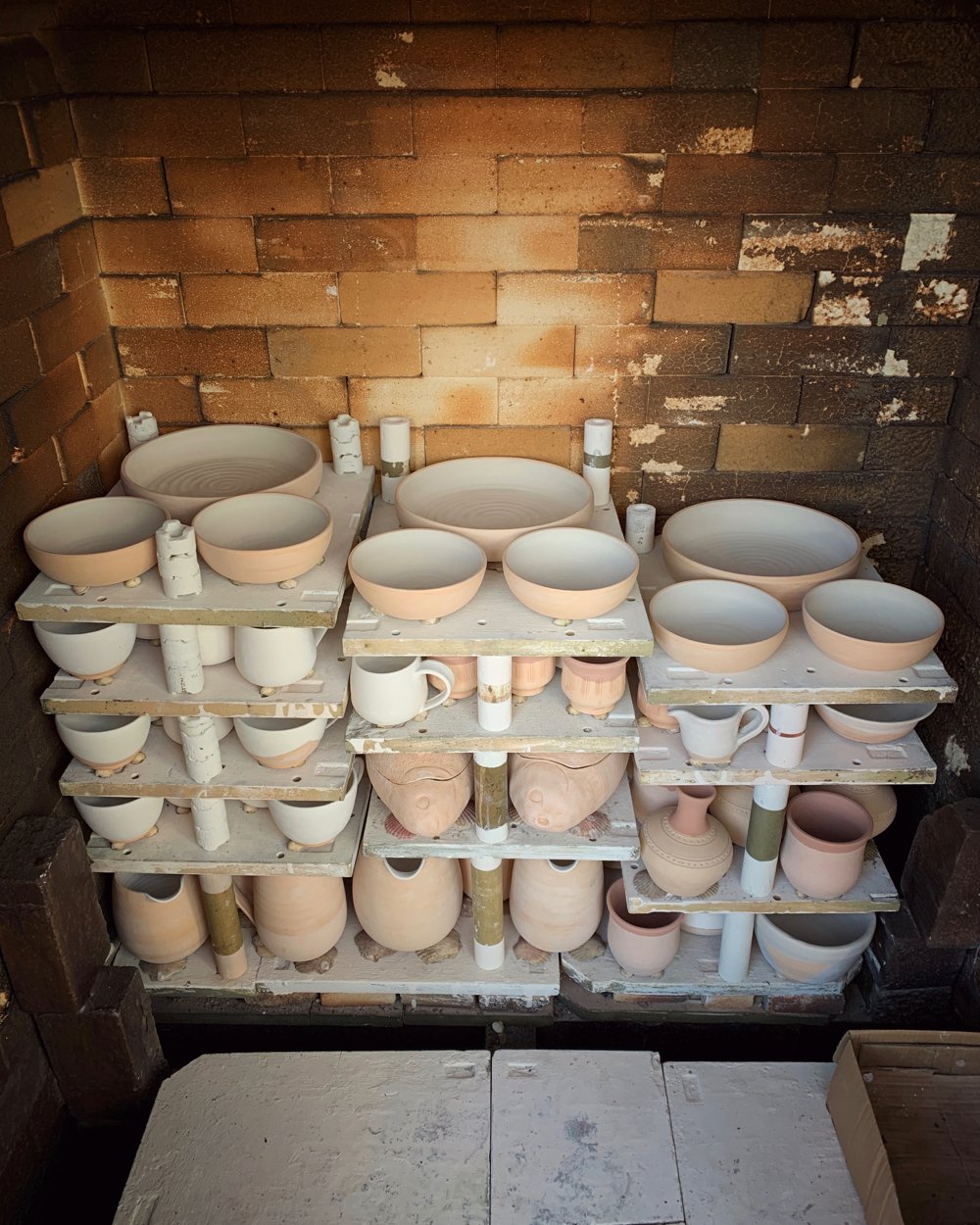


Each pot is balanced on three clay packed sea shells to stop them sticking to the shelf which then leave beautiful imprints on the clay.

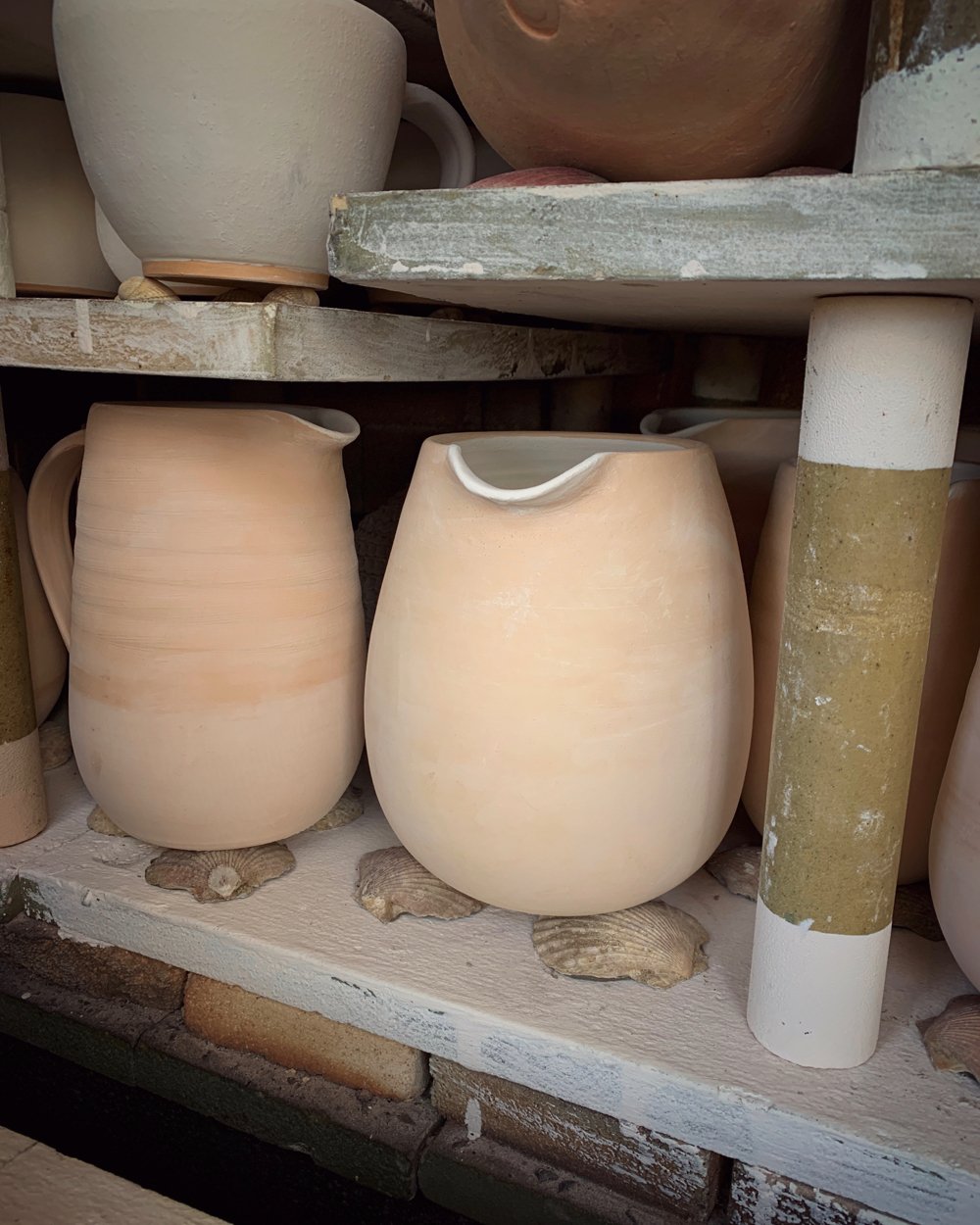
Finally the door is bricked up and temperature gauges fitted. Then the fun part begins …


The kiln is usually lit in the evening and kept at 200’C overnight with one member of the team checking every hour. This helps to pre-heat the kiln and dry any remaining moisture in the pots. Stoking in earnest starts first thing the next morning with the team working in shifts. The first 6-8 hours are usually straight forward as the kiln rises to 1000’C, but then it can take another 8 to 12 hours to reach 1280’C which we need for fully matured glazes. After an hour ‘soaking’ the glazes the team close down the kiln and head off to bed for a well earned sleep while we then wait for 48 hours before unbricking the door. The process is fraught with uncertainty as the kiln can be affected by weather and the ‘kiln gods’. There is always much trepidation on kiln opening day to see how they have faired.


Well apart from the obvious fun to be had playing with flames, the effects the kiln produces are both spectacular and unique. The wood ash landing on the molten glazes create beautiful speckles together with affecting the glazes flow, while the flames 'toast' unglazed clay.
Then there is the ‘reduction’ atmosphere, through varying the oxygen and fuel levels through the firing creating intense depth and variation to the glazes. Glazes will change depending on where they are in the kiln and in some cases change colour altogether, while iron in the clay is drawn out creating a russet hue to the clay body and speckles in the glazes. Whilst wood-firing is much more labour intensive that firing in an electric kiln, the results are really quite special - each pot will truly be a one off and completely individual.




Special thanks to Bill Crumbleholme who built our wood-kiln 'Woden, and is the true heart & soul of our wood-firing community.